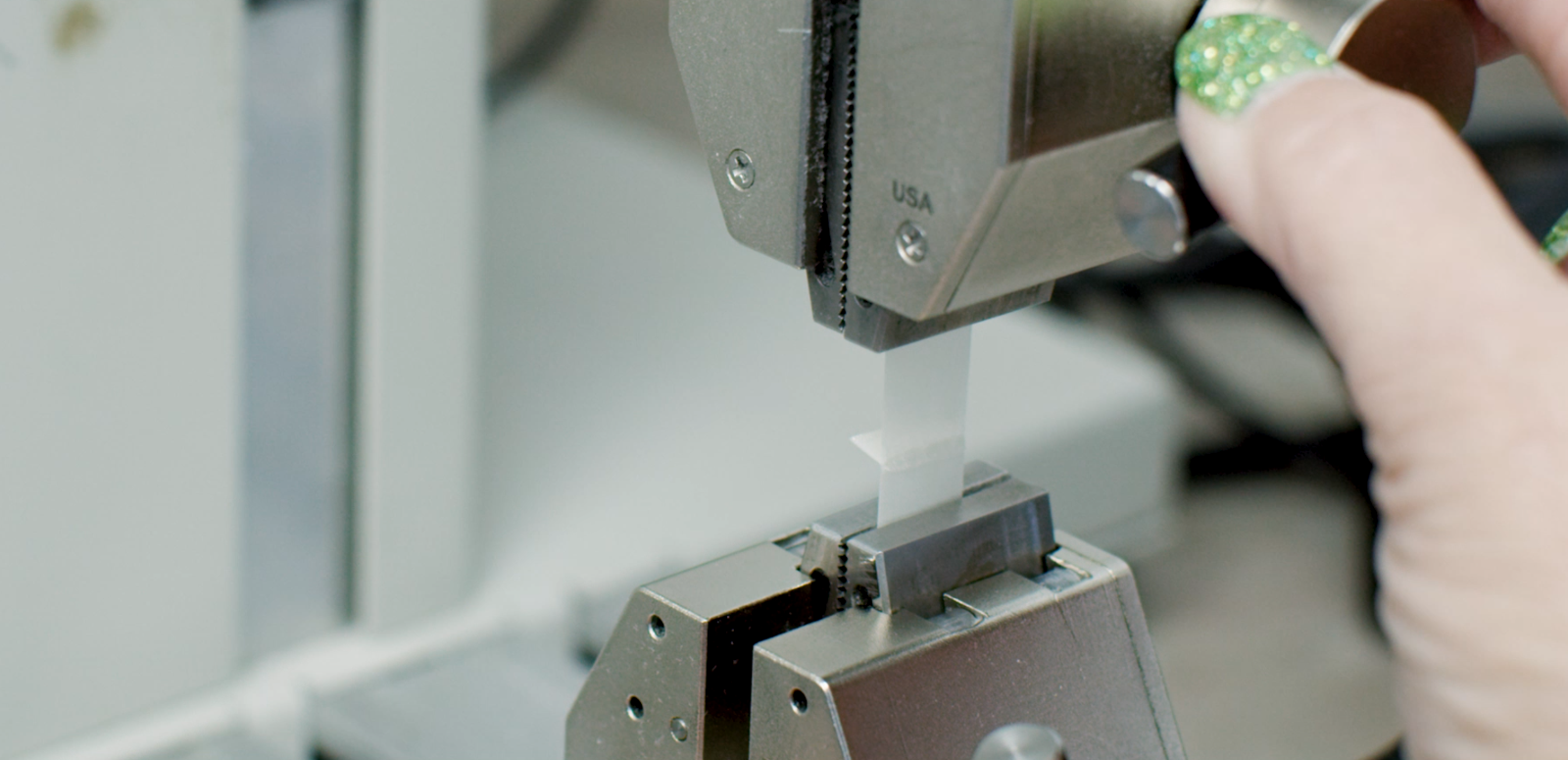
Polo Latest
Quality and Regulations in Manufacturing
This pulls excerpts from our podcast, Inspiring Innovation: Leaders in Manufacturing featuring Dawn Silver. To listen to our podcast episode, please subscribe to our channel on your favorite podcast platform.
Quality plays a vital role in all that we do at Polo Custom Products. When you are in the business of manufacturing products that can’t afford to fail, the first step is ensuring that products undergo rigorous quality testing procedures to guarantee they meet the standards set by our customers. Our total quality control is structured to mirror the way your product is used in the field. We must also be in compliance with a variety of regulatory requirements to continue to properly provide the highest quality output for our customers.
Regulatory Requirements Across the Industries
At Polo, we work with a broad set of industries, and each one may have their own regulatory bodies that we work with, such as the FDA, the FAA, and different automotive standards. All these regulations are similar even across the different industries in the purpose they serve, which is to ensure compliance. Our processes, our systems, and the way we manufacture products are partly controlled by the regulatory standards we have to comply with. However, there are differences when catering to products in different industries, such as the medical industry, automotive industry, or aerospace industry. What can be a challenge is making sure we are adhering to all the compliances that we need to while integrating them seamlessly into a single quality management system.
Here at Polo, we have built a fully functional and reliable quality management system that does exactly that. The purpose of our QMS is to improve our practices to better satisfy the needs and expectations of our customers, stakeholders and interested parties, and ensure processes are properly documented and controlled. Everything is documented thoroughly, including keeping processes up to date as changes happen. Everyone across the organization is regularly trained on quality procedures as they are updated, because at Polo, we believe that ALL employees belong in the quality circle. We believe that all employees play a vital role in quality, service, delivery and performance of our products.
Our Quality Management System
Polo’s existing quality management system was developed using ISO 9001:2015, ISO 13485:2016 and FDA QSR 21 CFR Part 820 as the framework. The first ISO standard for implementing a quality system is fairly generic and can be applied to multiple industries, such as service industries, manufacturing industries, health care industries etc. The second one, ISO 13485:2016, is unique to medical devices. The third part of our quality system is kind of built around FDA’s quality system regulation, part 820, which is also specific to medical devices. Being a custom manufacturer, there’s multiple industries that we serve, so there are also bits and pieces of other regulations that we incorporate into our QMS, such as aerospace and automotive regulations.
As was stated before, we believe that everyone belongs in the quality circle. Our system was built to ensure that all employees are successful in complying with our quality policy. And everyone at Polo fully supports the quality policy. Our entire staff not only ensures that the policy is implemented, but that it is also understood across all levels of the organization.
How We Measure Quality
Here at Polo Custom Products, we measure quality in two ways. The first way we measure is at the product level. This answers the important questions such as:
- Did we manufacture the product according to the customer’s specifications?
- Did we manufacture the product in accordance with our own internal standards?
- Did we comply with all the required regulations?
This is done utilizing various methods, which can include operator in process checks on the production floor, quality staff doing roving inspections, testing in the quality control lab such as functional and dimensional tests, and raw material incoming inspections. This is all monitored at the product level.
The second way we measure quality is at the quality system level. This answers questions such as:
- Is it effective?
- Does it meet the objectives it’s supposed to meet?
- Are there opportunities that exist for improvement?
We monitor several things on this front, such as customer feedback, customer satisfaction, customer returns and complaints, and defective parts per million (DPPM). Polo has maintained an incredibly low defective parts per million for 2023 at 138 DPPM, exceeding our corporate goal of 1200 DPPM. And while this is very impressive, it’s just part of the reliable quality assurance we work to achieve for our customers.
Quality Testing
Our products undergo rigorous quality testing procedures to guarantee they meet the standards set by our customers. This process is started early on in the product development stage and then continues all through production. At Polo, our preference is to mimic the way that our customers test their products. We duplicate that testing in-house whenever possible. This ensures there are no measurement discrepancies between the two.
As we move through design and development and that handoff into production, we create a master test device sheet. Those master test device sheets and inspection specification sheets will detail exactly how we will inspect a product and test it in production, as well as at what frequency.
At Polo, we utilize various testing methods for testing product and production. We have a dedicated quality staff that does this testing in a lab at each of our locations. Some of these tests include:
- Tensile Testing
- Pressure Decay Testing
- Inflation Testing
- Fitment Checks
- Dimensional Analysis
- Shake Testing
The Future of Polo
Polo is seeing unprecedented growth and will likely continue to grow and expand. From a quality perspective, this will come with additional regulations to meet and increasing capabilities to meet the needs of our customers. Technology may rapidly change the way we operate and approach quality management. But quality will continue to be at the forefront of everything we do. No matter what changes the future may hold, we will continue to provide the highest quality output for our customers.