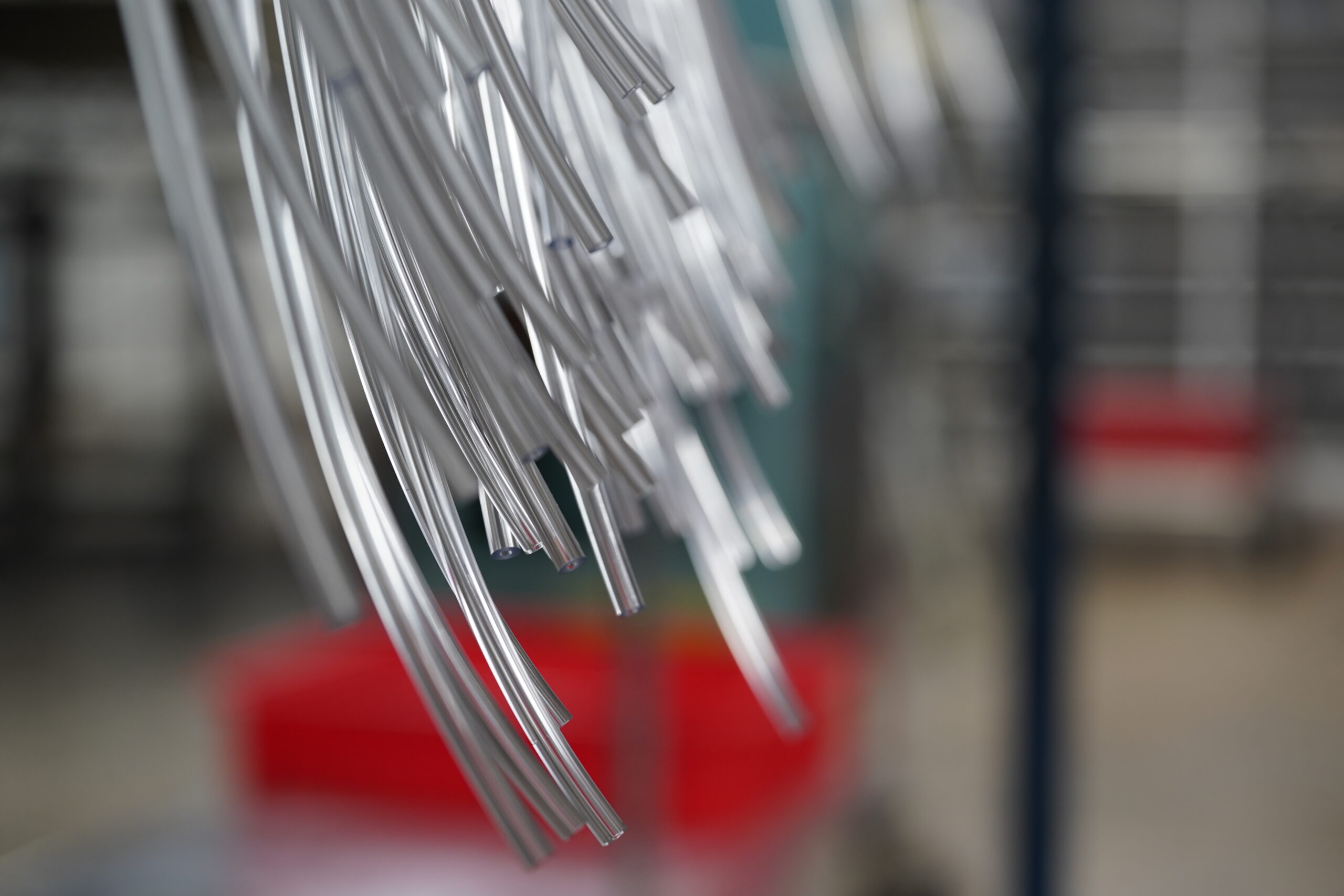
Polo Custom Products
Hot Air Welding
Choosing the Right Sealing Method
When it comes to sealing and bonding materials, there are several techniques to choose from. Each method has its own unique advantages and applications, making it essential to understand how they differ. Working with the Polo experts to choose the right method not only ensures the integrity and durability of the final product but also impacts production efficiency and cost-effectiveness.
Having a team like Polo on your side ensures you understand the unique characteristics and benefits of each sealing method. Our expertise is crucial for aligning your project’s specific needs with the most effective sealing solution, leading to a successful outcome.
Polo’s Sealing Capabilities
Polo provides a wide range of sealing techniques, expertly chosen to match the unique requirements of your project. Heat Sealing, Impulse Sealing, Ultrasonic Sealing and RF welding are methods that Polo offers. Each method has its distinct advantages that can fast track the trajectory of your products manufacturability.
Reach out below to learn about our Sealing Capabilities!
Polo’s Hot Air Welding Capabilities
Hot air welding is a manufacturing method that joins thermoplastic industrial fabrics and films by compressing and blowing hot air across electrical heat elements to apply and inject heat at the weld point. This technique is effective for materials with thermoplastic coatings and renowned for producing strong, durable seams across a variety of products. Constructing a product with different shapes and curves is easier using hot air welding. (Leave the RF welding section out since there are thick materials that are difficult to RF weld). The Hot Air Welding process involves directing a stream of hot air onto the surfaces of the materials, which are then pressed together to create a solid bond as they cool. Hot air welding is highly valued for its ability to deliver high-quality, consistent welds without needing additional adhesives. There are numerous applications for Hot Welding for example, but not limited to: large covers, dry bags, water resistant duffel bags, banners and awnings. It can be used with a range of materials and enhances efficiency in production. Some of the materials best suited for this technique include:
- Thermoplastic Industrial Fabrics and Films
- Polyvinyl Chloride (PVC): Commonly used in medical bags/tubing and packaging due to its good weldability and strong, durable joints.
- Polyethylene (PE): Often used in medical devices and packaging for its chemical resistance and flexibility.
- Polypropylene (PP): Valued for its high resistance to chemicals and high temperatures, making it suitable for medical components that need to endure sterilization processes.
- Polycarbonate (PC): Selected for its high impact resistance and clarity, ideal for transparent medical device components.
Click here regarding any sealing needs you have!
How can Polo Help You?
At Polo Custom Products, we offer comprehensive, cutting-edge manufacturing capabilities. We are always working towards continuous improvement and adapting processes as needed when customers bring us new and exciting challenges. Our commitment to precision, innovation, and quality is evident in all our processes. We’re fully compliant with ISO 9001:2015, ISO 13485:2016, and other quality standards and are dedicated to staying at the forefront of the
industry.
Please contact us with any questions or to request a quote!