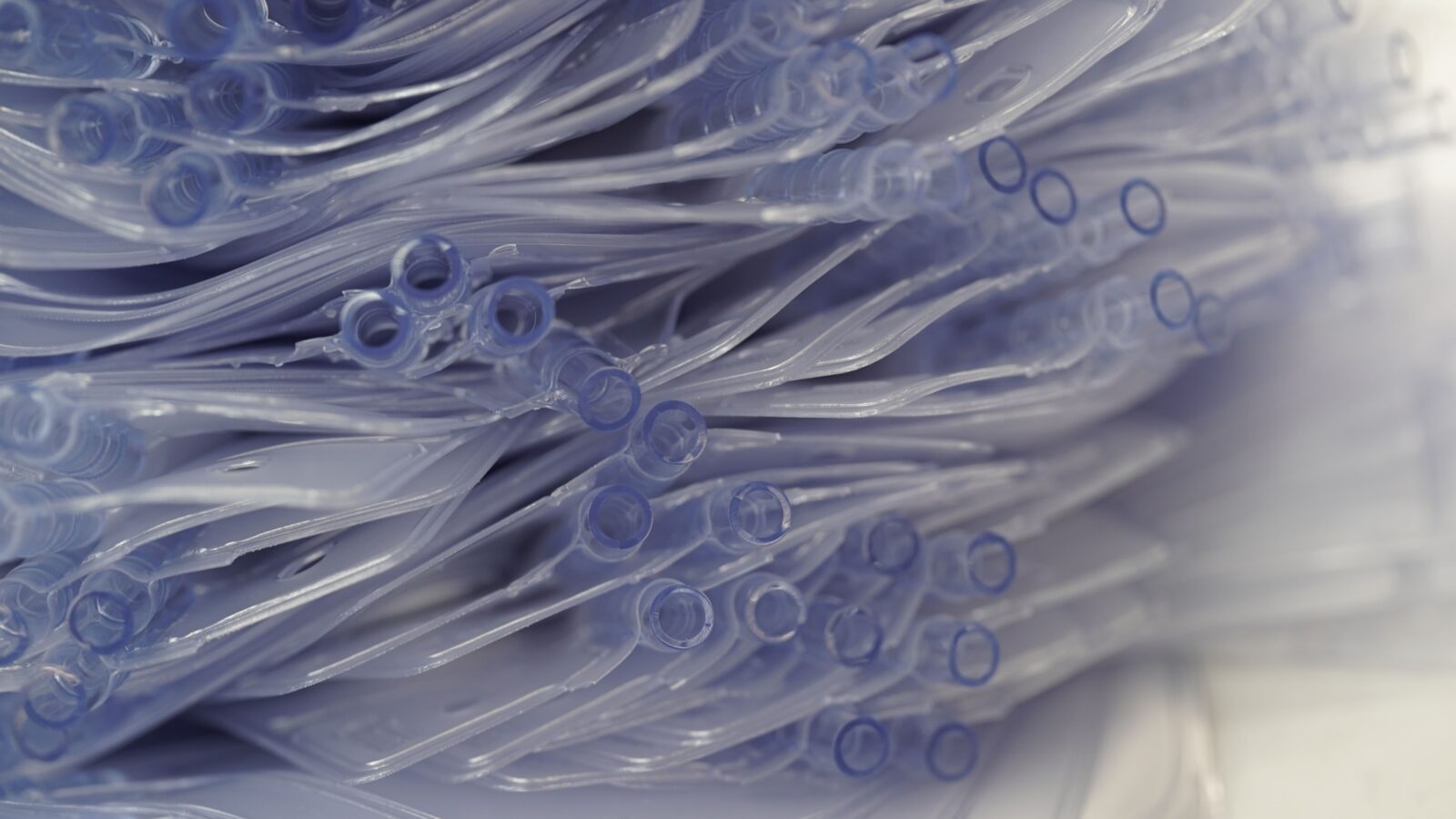
Polo Latest
Applications & Benefits of RF Welding
At Polo Custom Products, we utilize a variety of advanced manufacturing techniques to meet the diverse needs of our customers. When it comes to medical products, we leverage the precision and reliability of RF welding to ensure our plastic components meet the stringent quality and safety requirements of the healthcare industry. From IV bags to blood pressure cuffs, our RF-welded products are designed to support healthcare professionals and enhance patient care with high-quality, sterile solutions.
RF Welding Explained
RF welding, also known as dielectric or high-frequency welding, is a state-of-the-art process to fuse or seal plastics. High-frequency waves generate electromagnetic energy capable of welding plastic surfaces precisely.
The RF Welding Process
RF welding uses radio frequency waves, typically at 27MHz, to create sufficient heat in thermoplastic materials to reach the melting point of the material. At the same time, the welding tool applies constant pressure to both plastic components. As the plastic surfaces melt, they fuse. Once cooled, the finished product has a solid, leakproof seal.
Advantages of RF Welding
RF welding offers several advantages:
- Permanent Seal: Unlike adhesives that can eventually dry out and weaken, RF welding fuses plastic surfaces and creates a seal that’s as strong as the original material.
- Watertight & Airtight Products: The RF welding process delivers products that are completely watertight, waterproof, and airtight, such as fluid pouches.
- Industrial-Strength Welding Options: By heating plastics from the inside out, RF welding provides a strong seal even with thicker layers, ensuring reliability.
- No VOCs: RF welds don’t use any solvents, glues, or other volatile organic compounds.
RF welding is also cost-effective, fast, and flexible.
Industries That Use Radio Frequency Welding
Any industry that needs sealed plastic products can benefit from RF welding advantages. Commercial and industrial applications include airline oxygen masks, tents, airbeds, life jackets, inflatable rafts, pool covers, and heavy-duty air hoses.
RF Welding Applications in the Medical Industry
The healthcare industry relies extensively on plastics. RF welding is involved in countless products for hospitals and clinics, including:
- Medical Class I and Medical Class II drainage bags
- Fluid collection bags
- IV bags
- Colostomy products
- Laparoscopic surgery specimen collection bags
- Blood pressure cuffs
RF-welded products help to lower supply costs while maintaining a sterile environment for patients.
Materials That Are Compatible with RF Welding
RF welding applications are compatible with thermoplastic materials with a bipolar molecular structure (dipole), such as:
- Polyvinyl chloride (PVC)
- Thermoplastic polyurethane (TPU)
- Nylon (Additional specifications required for this material)
In certain situations, RF sealing technology can also fuse non-polar thermoplastics, such as polyethylene terephthalate (PET) and low-density polyethylene (LDPE).
The Potential of RF Welding Technology
Current-generation RF welding for medical devices requires large equipment and specialized CNC software. As this technology advances, manufacturers can look forward to a greater level of customization, lower production costs, and enhanced flexibility for complex geometries.
Experts in RF Welding for Medical Devices
At Polo Custom Products, we are at the cutting edge of RF welding technology. We engineer and create custom plastic products for the medical industry. We’re fully compliant with ISO 9001:2015, ISO 13485:2016, and other quality standards. Request a quote for detailed information on our capabilities.